Developed by an interdisciplinary team of researchers in MIT’s Media Lab and Northeastern University led by Media Lab PhD student Jack Forman, FibeRobo is a body-temperature-responsive fiber derived from the use of liquid crystal elastomers (LCE). This new material has the ability to undergo self-reversing morphing precisely at, or slightly above, body temperature due to a new fabrication technique developed by the research team alongside the chemical composition of the fiber. The fibers can then be formed into larger textiles through a number of standard processes, including knitting, weaving, and various sewing techniques for use in a wide range of industry applications from everyday wear to medical devices.
“We use textiles for everything. We make planes with fiber-reinforced composites, we cover the International Space Station with a radiation-shielding fabric, we use them for personal expression and performance wear. So much of our environment is adaptive and responsive, but the one thing that needs to be the most adaptive and responsive — textiles — is completely inert.”
- Jack Forman, lead researcher and graduate student in the Tangible Media Group of the MIT Media Lab
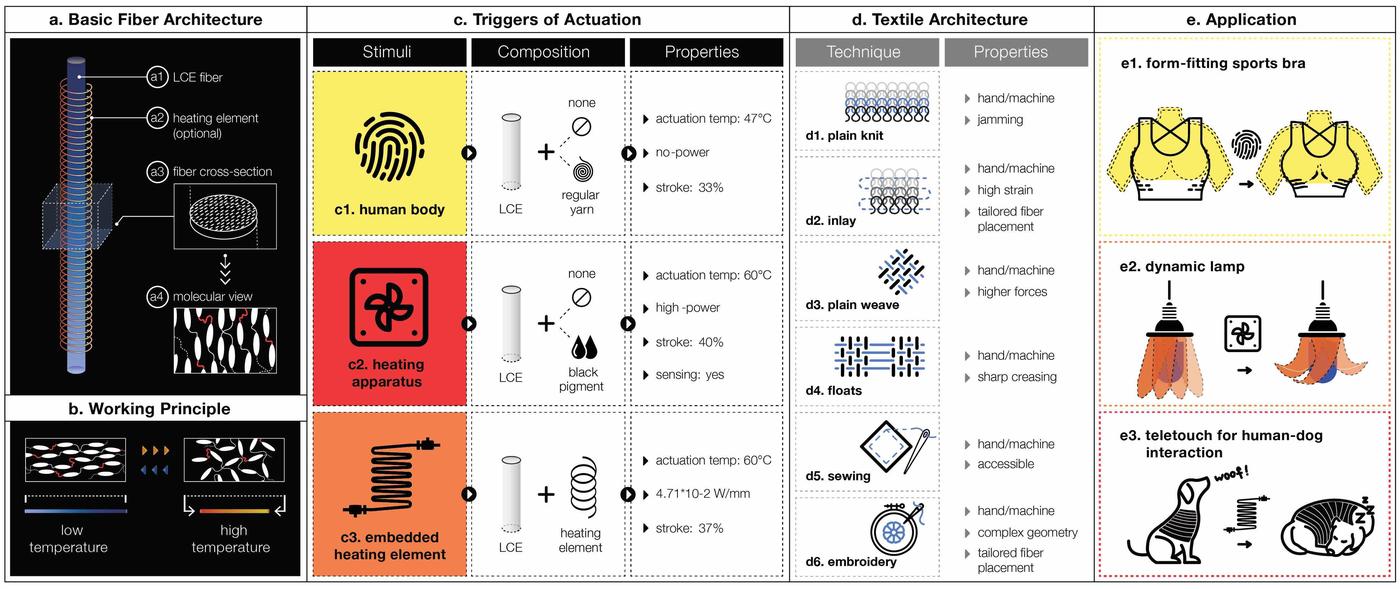
The performance of FibeRobo stems from its composition of LCE, a fusion of crystal-like structure and liquid flexibility. When subjected to heat, the LCE's crystal molecules realign, causing the fiber to contract. The fiber can expand up to 40% without bending, and upon cooling, it reverts to its original length. During the manufacturing process, the viscous LCE resin is heated, extruded through a nozzle, and finally cured with UV light. This adaptable fiber can then be integrated into existing textile production methods, as previously mentioned.
FibeRobo's potential applications are diverse and widespread across numerous industries. MIT researchers have showcased its effectiveness in adaptive sports bras and compression jackets for dogs, underscoring its versatility. Additionally, applications may include post-surgical compression bands aiding in blood circulation and athletic wear changing form based on the level of physical exertion. Notably, the MIT team is actively pursuing recyclability and biodegradability for FibeRobo components for sustainability. The potential impact of this responsive textile, which can adapt to either environmental or physiological conditions, cannot be understated, from improving quality of life to shifting the ways in which we behave and interact in the built environment.
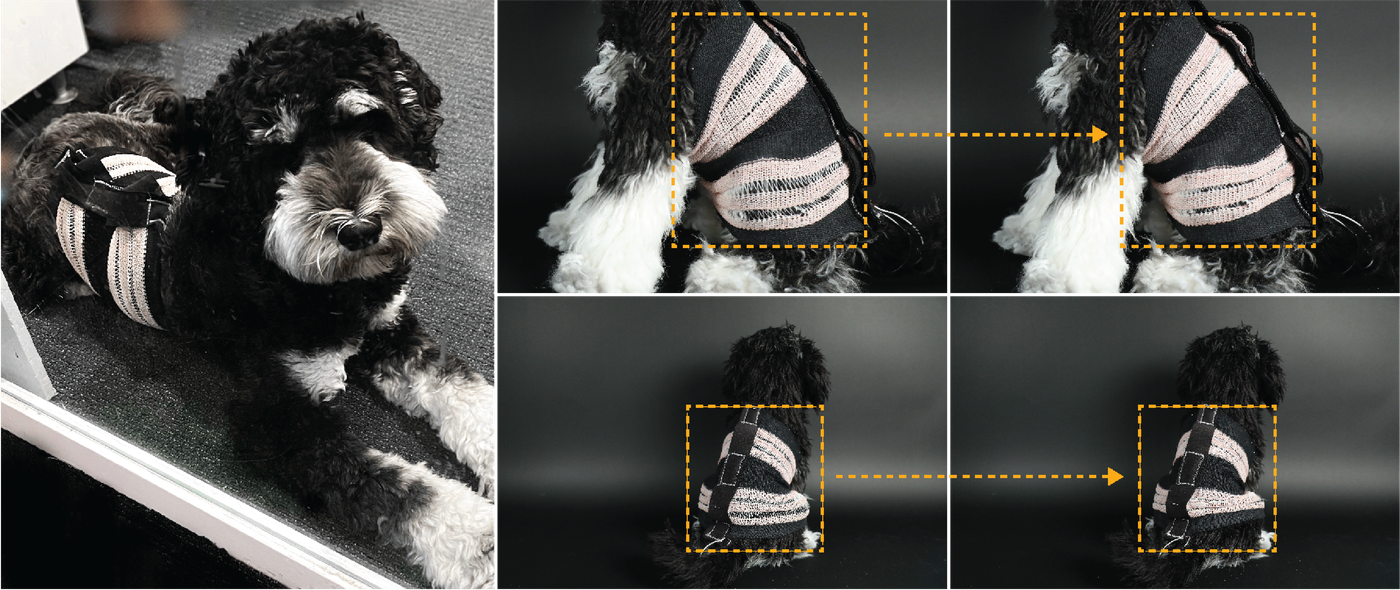
Is this new material cost-effective? According to the researchers, yes! At one-sixtieth the cost of commercially available shape-shifting fibers, FibeRobo can be manufactured for approximately 20 cents per 3.28 feet. The relatively low cost of FibeRobo’s production, coupled with its compatibility with standard textile manufacturing processes such as weaving looms, embroidery, and industrial knitting machines, makes this an accessible option for smart textile applications beyond the immediately visible applications in fashion and medical devices. For example, the highly adaptive, self-actuating, and sensing capabilities of textiles produced with fiber lend themselves well to applications in electronic textiles. By incorporating conductive threads, digital triggers could be integrated into textiles wherein reading such as light, dust, and proximity sensors. Using electro-thermal actuation can enable textiles to adapt their shape based on such digital triggers (among others).
The development of this new material and fabrication process could have an impact on not only our everyday clothing but also lead to major advancements in sectors like medicine, sports, and aerospace engineering.
This is a significant leap forward in the area of smart textiles.