During the last decade, biodesign and biofabrication have emerged as a new disciplinary domain at the intersection of design, biology, material studies, and engineering. The growing interest and push to move away from petroleum-based and animal-derived materials towards those stemming from the cultivation of microorganisms like algae, fungi, and bacteria has been driven by a need for sustainable solutions to complex environmental issues coupled with technological advancements. The potential widespread impact of this domain on everything from fuel, food, and clothing to cosmetics and construction materials is extensive.
In a 2017 article by Fast Company, Meg Miller posed the question of whether biodesign would become a new design discipline or if the principles and practices within the then-emergent area would be integrated across design disciplines at large, particularly industrial design. Five years later, perhaps both can be true.
In addition to biomaterials and biofabrication processes being adopted across industries, biodesign has become a staple area of study within universities and colleges, internationally. As recently as 2019, it was announced in Dezeen, that Central Saint Martins University of the Arts London would be launching its Master’s degree in sustainable innovation, “explore[ing] bio-informed design strategies in a bid to encourage more eco-friendly focused innovation,” with the central aim “to rethink the approach to design and manufacturing by engaging with biological systems in architecture, product design, jewellery, fashion or textiles.” At that time Central Saint Martins claimed it was the first such academic program. Fast-forward to 2024, undergraduate and graduate courses are offered in universities and colleges around the globe, including University College London, Newcastle University, Stanford University, and the University of Melbourne, and the list goes on.
The integration of biodesign and biofabrication across industries, including healthcare, fashion, and construction, is increasingly pervasive. In the healthcare sector, biofabrication are driving advancements in regenerative medicine, personalized healthcare, and medical device manufacturing. Organovo is an early-stage medical laboratory and research company that designs and develops functional tissues that closely mimic native human tissues. These biofabricated tissues can accelerate preclinical drug trials, disease modeling, and tissue transplantation. Stryker Corporation, a leading medical technology company, works with additive manufacturing, including bioprinting, to produce patient-specific implants and surgical instruments. Stryker produces customized medical devices to match the unique anatomical features of individual patients, improving surgical outcomes and patient care.
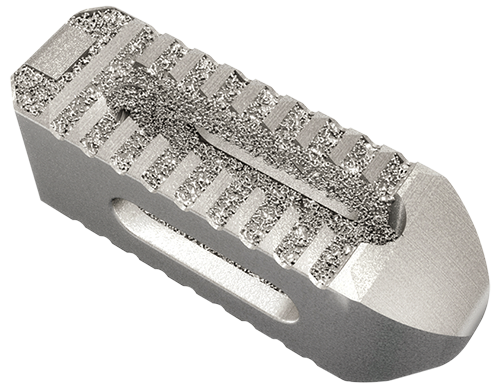
Numerous developments have been made in the fashion industry with alternatives to conventional textile manufacturing processes that rely heavily on petrochemicals and water-intensive practices. Bolt Threads, a biotechnology textile company, developed Microsilk™, a synthetic silk protein produced by engineered yeast cells. This biofabricated silk offers a cruelty-free and sustainable alternative to traditional silk production, which involves harvesting silk from silkworms. Adidas collaborated with Bolt Threads to produce the Futurecraft Biofabric shoe, which is made from biodegradable material derived from microbial fermentation.
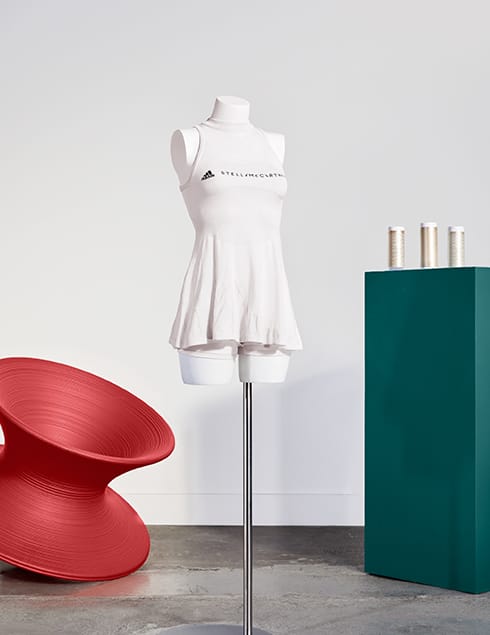
Modern Meadow's biofabrication process involves growing collagen-producing cells in a lab-controlled environment, resulting in a material that closely resembles animal leather in look, feel, and performance. By circumventing the need for animal farming, Modern Meadow's biofabricated leather offers a more ethical and environmentally friendly alternative to conventional leather production. In 2023 Modern Meadow partnered with the iconic brand Ella to launch a few version of the Tory Burch classic tote bag using Bio-Tex™.
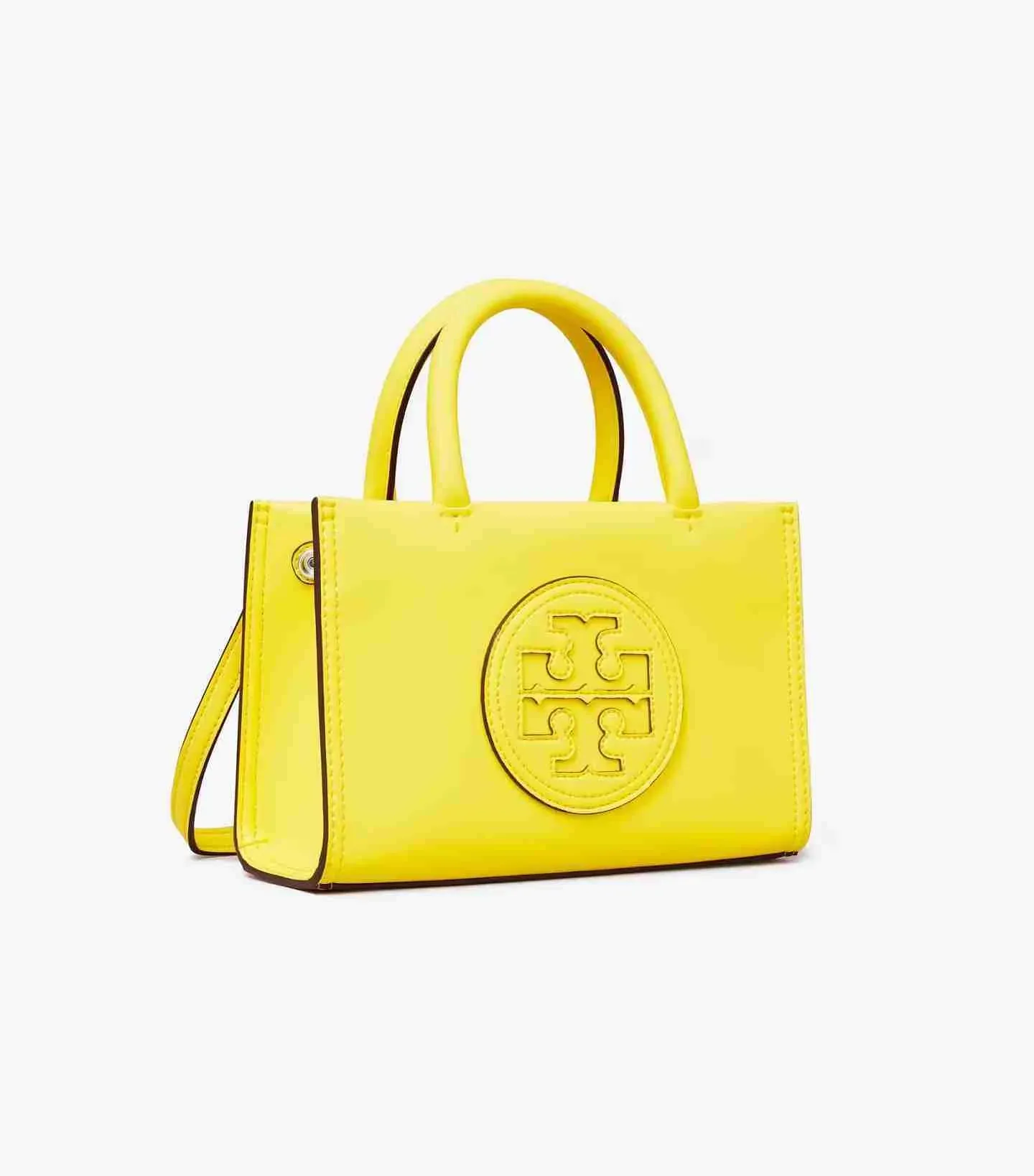
Similarly, biodesign and biofabrication are paving the way for the development of sustainable building materials in the construction industry. One noteworthy example is BioMason, a company using bacteria to grow biofabricated bricks. BioMason's process involves exposing sand and nutrients to bacteria, which produce a natural cement that binds the sand particles together, forming solid bricks. This biofabricated building material eliminates the need for high-energy kiln firing, reducing carbon emissions and energy consumption associated with traditional brick manufacturing.
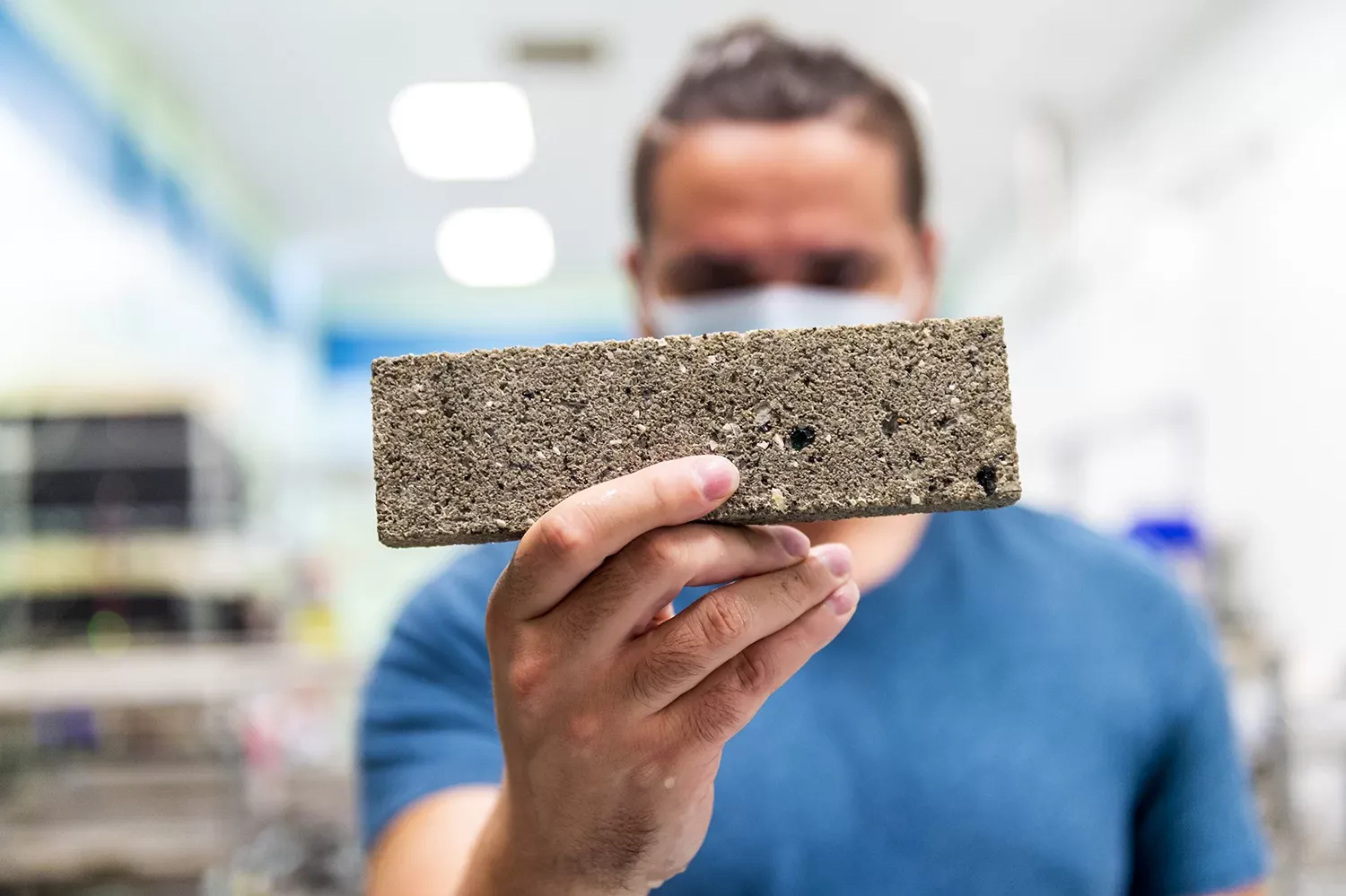
Ecovative Design specializes in biofabricated insulation materials made from a material extensively explored in biofabrication: mycelium, the root structure of mushrooms, which serves as a natural binder for agricultural waste fibers. These biofabricated insulation materials offer superior thermal performance and environmental sustainability compared to conventional insulation products, which often contain synthetic chemicals and petroleum-based materials.
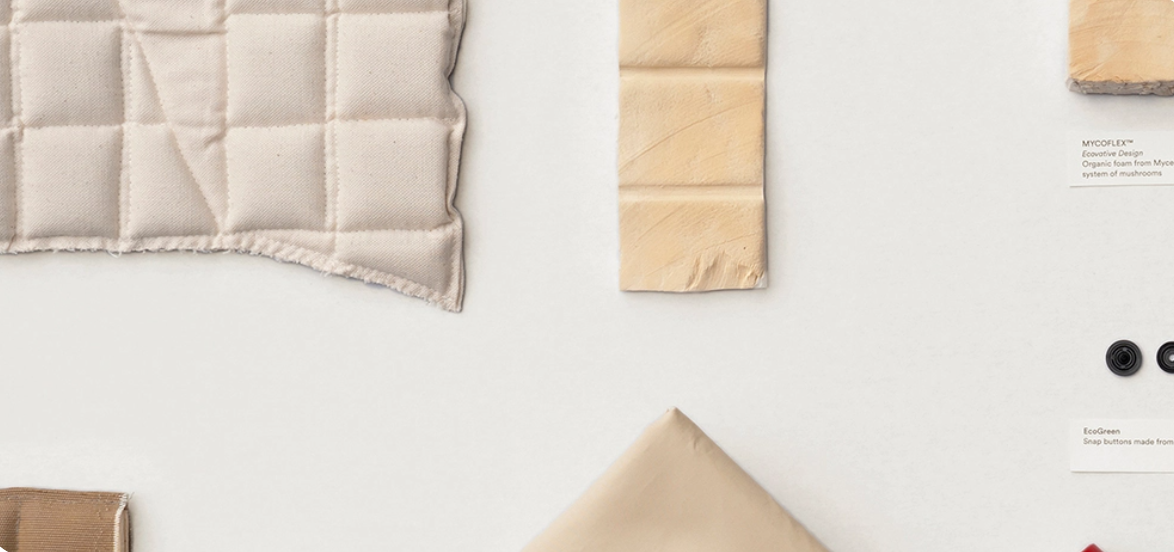
Reflecting on the evolution of biodesign and biofabrication over the last several years, it becomes evident that its influence is permeating diverse sectors at an accelerating pace. What began as a speculative inquiry into the future of design has transformed into a fundamental aspect of academic curricula worldwide and substantive integration across industries. Driven by a global need to identify sustainable solutions to address environmental issues and advancements in technology, the domain of biodesign and biofabrication has rapidly emerged as both a bespoke stand-alone discipline and a design ethos at large.